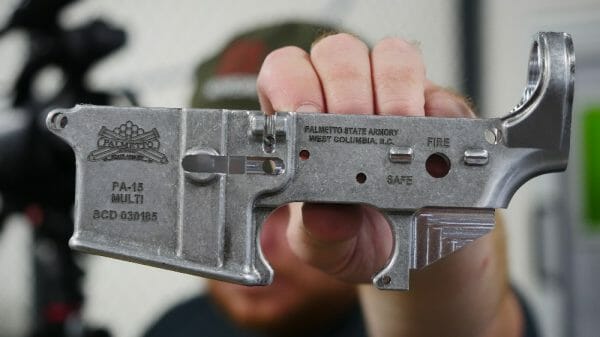
U.S.A. –-(Ammoland.com)- Have you ever wondered what goes into a Palmetto State Armory rifle? I have. Since Duncan and I were invited to visit with them and tour their facilities, we were about to get a first-hand look at how the rifles, uppers, and other parts are produced.
Duncan and I flew out from our home bases to Charleston, North Carolina and met with Josiah McCallum, the Affiliate Marketing Manager and co-founder of Palmetto State Armory, at the airport for the long trek to Columbia, South Carolina where Palmetto State Armory is based.
After getting checked into the hotel and settled, Duncan and I grabbed a bite to eat and planned out how we were going to tackle writing the tour up since we had an insane schedule.
NOTE: Some areas of the tour were not photographed or videoed to protect trade secrets so your imagination will have to suffice, sorry.
DC Machine
The first stop on our grand tour of the PSA facilities was DC Machine, the facility that produces not only PSA’s barrels, but they also make lower receivers, upper receivers, barrel extensions, receiver extensions and a ton of other stuff that makes its way onto PSA rifles.
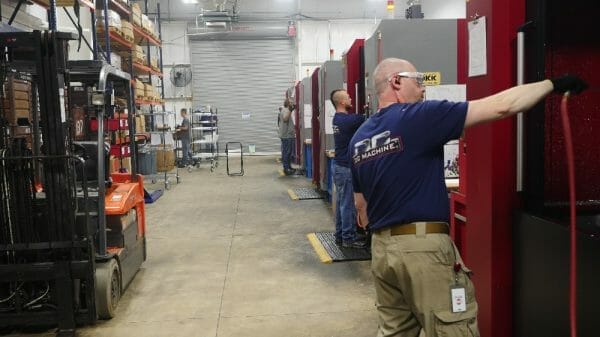
While we were in the car with Josiah, we got the rundown on the history of the company as well as a good feel for the mission of PSA. They want to put a serviceable rifle in the hands of every American, a noble goal if we are honest. More gun owners inevitably lead to better gun rights and more 2A supporters.
The staggering number of barrels that they are able to produce daily is nothing short of awes inspiring. 1,800 new barrels are born a day in this facility on top of the many upper and lower receivers making the level of QC that they achieve pretty impressive.

DC Machine has over 70 CNC machines that run almost non-stop to feed the beast that is Palmetto State Armory, and that isn’t even enough to satisfy their needs.
While Duncan and I were at DC Machine, we were given the two newest barrels off the line. Later those barrels would be built into rifles by us in their assembly facility.
PSA Flagship Store
While PSA has its largest presence on the internet, they do have 6 physical stores where you can shop their selection in person. While this is a pretty cool experience, it is also just as dangerous for your wallet as the daily deal section of their website.
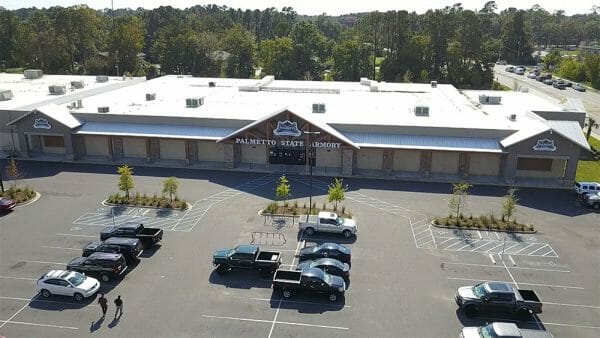
While we got the tour of the store and range, we also were there to do some light shopping for optics that would be used on the rifles we were to build. I opted for a Vortex Strike Eagle paired with a Trijicon RMR to give the dual optics setup a try while Duncan chose the more 3 Gun orientated Vortex Viper PST Gen II 1-6 power scope.
I will have to admit, I was rather pleased by my experience in both of the stores that I visited. Now you might be thinking that since Duncan and I were there as guests of PSA that is why they were on their best behavior. I will confess to wandering off several times to see how the staff interacted with customers as well as myself and had to say that it was nothing short of impressive for a brick and mortar gun store. The staff was friendly, knowledgeable, and eagerly helpful.
As for selection, the stores somehow have MORE stuff than the website! Pretty much anything that I was looking for, they had in stock and at reasonable prices. The selection and how they had stuff priced is probably why I spent far more money than I intended on while taking a tour of the store.
After we were done with the store tour, we headed back to Columbia where I asked Josiah to drop me off at a local range so I could get a bit of practice in with my Glock 19. I will talk more about why later but I am very appreciative that Josiah accommodated my need to get some practice in while on the road.
View this post on InstagramA post shared by Patrick Roberts (@thepatrickroberts) on
Touring the Main Warehouse
We got the full tour of the impressive facility where Palmetto State Armory ships all of their web orders from as well as assembles ever upper, lower, and complete rifle at.
While I wish that I had taken some photos of the facility, much of what I wanted to show I wouldn’t have been able to share in good conscious like steps in the assembly process and secure areas like the gun room. Rest assured that the entire facility was nothing short of impressive, the most impressive thing I saw was the AR assemblers.
The assembly area has a couple of different sections, each working on different areas of the rifle or even an entirely different platform like their AKs. I want to touch briefly on the AK rifles before we get into the ARs that PSA is most well known for. I intend to go back and spend a ton of time looking at how the AK platform parts are sourced and assembled. I really want to show you all as much about the manufacturing process as they will allow for the simple reason that I feel most don’t understand exactly how good of a rifle they are without seeing one come together. The fact that they are producing what appear to be reasonably high-quality US made AKs for under $1,000 is nothing short of impressive when you understand the hurdles that US made AKs face.
The AK team at PSA is a well-oiled machine that makes putting an AK together look like child’s play. As I previously mentioned, they use quality parts from what I could see and assemble them systematically and efficiently. What was the coolest thing about the process? The way the barrels were installed and head spaced. I wish I had a photo to show you, but that will have to wait until I can cover the build process in far more detail on my next visit.
Now that we have the AKs out of the way, the AR assembly line is likely what most people care about. Again, PSA has worked with some amazing process engineers that have developed an efficient assembly line that allows for near no QC issues to slip through. After all, with the volume of uppers, lowers, and rifles that PSA is sending out to Americans everywhere, there is bound to be a couple of small things that slip through the cracks. Don’t worry though, they have a process to identify who built any components or rifles that weren’t up to snuff and stressed that they will do everything in their power to improve the assembly process. That said, the percentage of components that experience an issue are staggeringly low. While I don’t recall the figure offhand, I do recall that when I heard the number, it was substantially lower than any other facility that I have had the pleasure of visiting.
The upper receiver process starts with the forward assist being pinned in place by a single station. The engineers at PSA designed an impressive jig to ensure this pin is placed in the upper uniformly. Once that is done, and the dust cover is installed, the uppers are sent down to the assembly stations. If the upper build calls for a front sight post, the FSP, delta ring, and any needed hardware is placed on the barrel and is drilled for the taper pins on a CNC machine and the taper pins are put in place.
Now that we have the barrel and upper ready to mate at the assembly stations one of the skilled assemblers gathers all the parts they need to finish the upper build. They have their own upper blocks that were designed by one of their engineers that makes the process easy and fluid. Once the upper receiver is pinned to the block, they insert the barrel, apply some grease to the threads and tighten the barrel nut. Once that is done if the build has an FSP the assembler checks to make sure it is aligned properly with yet another special tool. They add the gas block if needed and install the gas tube then the flash hider or brake is attached to the barrel and timed properly. Now is the time that the assembler either slaps on some plastic hand guards if the build calls for that or secures the free float handguard to the upper. Once all that is left is to add the charging handle and BCG, the upper is tilted up so that the assembler can stamp their mark on the upper. This stamp allows PSA to track who built what and ensured that any problems that are returned are addressed by not only making it right with the customer but also training the assembler to look for that issue going forward.
The assembly of the lowers is equally impressive. Where the upper assemblers have special tools to help them produce the best possible product in the quickest manner possible, the lower assemblers have developed nimble fingers, and ways of installing parts that help prevent them from damaging the finish on the lowers as well as retain all the parts they need to build the lower. The lower starts as striped and one worker installs all of the lower parts but leaves the buffer tube untorqued and the endplate unstaked. That particular part of the build process is completed by another worker at a separate station. While the lower build process is just as impressive as the upper build process, the number of steps required is far fewer.
Every PSA upper, lower, or complete rifle is either function checked in the case of lowers or test fired in the case of uppers or complete rifles. This is done on site in a test range located just off the assembly area.
At the end of my tour, I have a newfound respect for PSA’s rifles that I frankly didn’t have before visiting their assembly facility. It wasn’t that I thought that PSA didn’t make decent rifles, it was more than I had no idea that they were building rifles to the quality level that they are. Everyone there cares deeply about putting out the best possible product to be sold at an attainable price point. Every single employee that I spoke with believes in the PSA mission of putting a rifle in the hands of every American that can legally own a firearm.
Read Part 2 of the Tour Tomorrow
Special Thanks
I want to thank Josiah and everyone else that either spoke with us on the tour or made it happen. The hospitality shown was nothing short of above and beyond what anyone would expect on a media trip.
I am looking forward to making my way back to Columbia for the next visit!
About Patrick R.
Patrick is a firearms enthusiast that values the quest for not only the best possible gear setup but also pragmatic ways to improve his shooting skills across a wide range of disciplines. He values truthful, honest information above all else and had committed to cutting through marketing fluff to deliver the truth. You can find the rest of his work on FirearmRack.com as well as on the YouTube channel Firearm Rack or Instagram at @thepatrickroberts.
The post Ammoland’s Epic Tour of Palmetto State Armory – Part 1 appeared first on AmmoLand.com.
via AmmoLand.com
Ammoland’s Epic Tour of Palmetto State Armory – Part 1