https://www.recoilweb.com/wp-content/uploads/2021/05/replacing-pistol-sights-11.jpg
Most handguns come with factory sights that are pretty rudimentary, and they’re often the first thing to be replaced. Perhaps you want to see your pistol sights better in diminished light, to acquire them quickly in bright daylight, to use them to rack the slide, or even to adjust them on the fly. There are many aftermarket options for most pistols; find one that best suits your intended use of your handgun.
If you plan on shooting competitions at your local outdoor range, a thin, front fiber-optic sight might work best. However, if you also want to take the gun to tactical shooting courses where you’ll be racking the slide off barricades and treating
your gun like a Harbor Freight tool, you might want something a bit beefier. Choose pistol sights that are a good fit for you, because even a great handgun can be ruined with a poor aiming system.
BASICS
The majority of pistol sights are secured in a dovetail cut — an isosceles trapezoid shape cut from left to right with the long side at the bottom, creating two angled overhangs that prevent the sight from moving up and down or fore and aft. Let’s discuss how to remove your old sight and install or “drift” in new ones.
Most sights are considered “drop-in” parts, which can be installed without any customization. However, slight fitting is sometimes required. When removing material to install sights, fit the sight to the gun, not the gun to the sight. Also, never touch the bottom of the sight dovetail. There should always be a slight gap between the underside of the sight post and the top of the slide; removing material from the bottom of the dovetail will pull the post downward, interfering with the top of the slide.
TOOL SELECTION
There are many gadgets available to install sights. “Universal” sight pushers can be handy but also rather expensive (upward of $100), and often not quite universal. Dedicated sight pushers aside, you can remove and install sights with some basic tools:
Sturdy vise: If you intend to work on firearms, a good vise is a must, preferably with at least 4-inch jaws. It should be hefty, so that when you clamp it down on something and hit it with a hammer, the vise won’t flex. This ensures all the force is transmitted to the workpiece; otherwise, it’s like trying to crack walnuts with a hammer on a mattress. When mounting a vise to a bench, try to locate it on a corner, directly above the leg, for maximum rigidity. Most vises come with scored jaws that bite into wood and rough material but will damage your slide’s finish, and a couple layers of tape won’t protect your bluing or Cerakote. You can take the jaws to a machinist to smooth off the texture or use soft jaws.
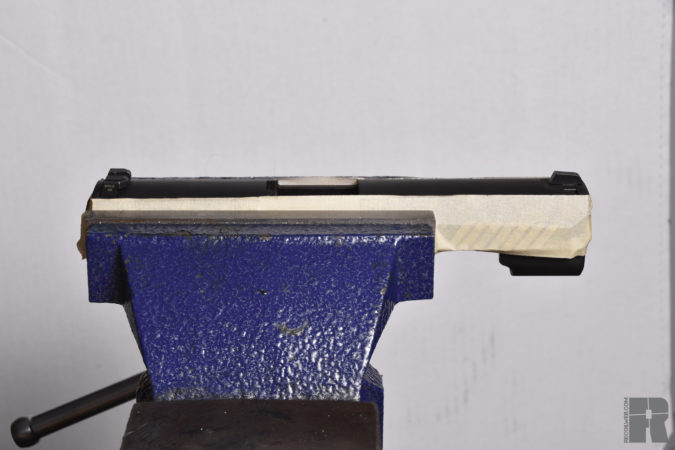
A layer of masking tape gives a little protection to your slide’s finish, or in the case of a HiPoint, prevents it from getting crap on your vice.
4-ounce ball-peen hammer: This hammer might seem dainty, but it’s the preferred striking weapon of gunsmiths for a reason. It allows much more control and finesse while keeping you out of trouble. Keep the flat face dressed with a stone to ensure good perpendicular contact and to avoid glancing hits, which can lead to shattered punches or uneven contact on the punch face.
Drift punch set: There are many different types of drift punches for drifting sights, but it’s hard to beat a simple set of steel Starrett punches. Nylon-tipped, brass, and most aluminum punches are too soft and require extra force to finely control small movements of the sight, often causing them to flex or compress.
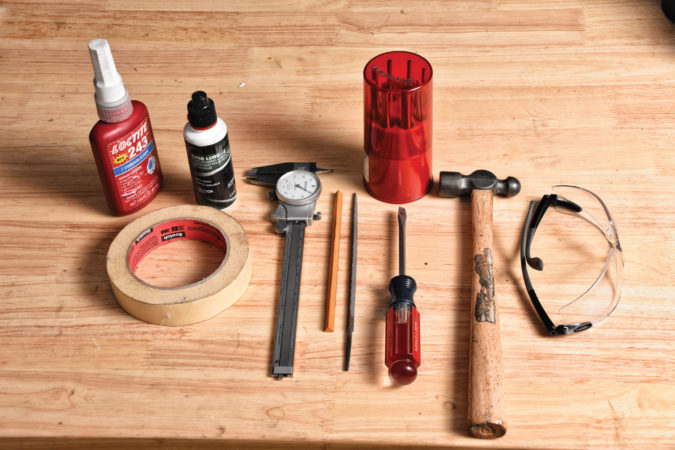
If you’re going to start messing with sights (and on stock Glocks, we should really put that in quotes), then you’re going to need a few basic tools.
Fine triangle file: Hopefully, your slide cuts and the sight’s dovetail will be the perfect size for a slight interference fit, allowing for hassle-free installation and solid retention. When fitting is needed, use a fine, single-cut triangle file that cuts smoothly while taking a minimum of material. Grind one side of the file smooth to use as your “safe” side. If the sight is a 60-degree dovetail, use the bottom of the sight post as a guide for a consistent, clean cut. If you have one, a triangle India stone is also handy for dressing the dovetail.
6-inch calipers: Dial or electronic calipers allow you to precisely position the pistol sights on the slide. While not as accurate as a depth micrometer, the depth rod on the tail of the caliper will get you within a couple thousandths.
REMOVAL
Before you start, put on eye protection, then unload your pistol, making sure to remove the magazine and clear the chamber. Then, remove the slide, recoil spring, and barrel. Attach a strip of painter’s tape on the slide flats on each side just below the sight dovetails, to provide some protection.
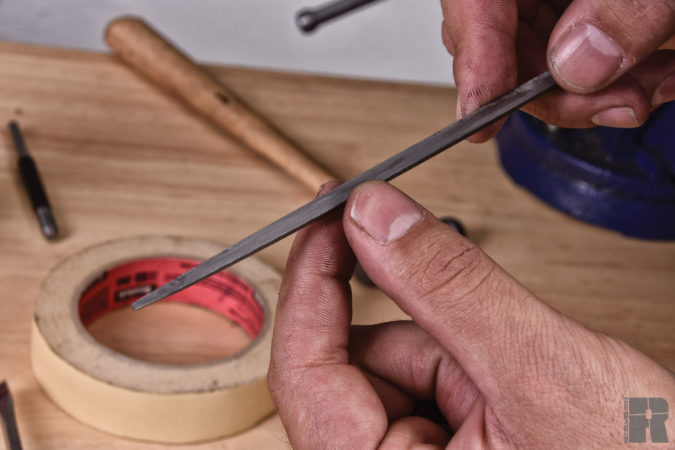
If you care about your handgun, grind a safe edge on your triangle file so that it only cuts on one surface at a time.
Carefully inspect both the top and the bottom of the slide around the sights. Some factory sights are further retained in the dovetail with a set screw or vertical roll pin. If so, carefully remove them. If you have an elevation-adjustable rear sight, remove the adjustment screw and spring, tilt it up to check for additional set screws underneath, and remove those as well. Make sure to use the proper hex wrench to avoid stripping them. If you suspect there’s any threadlocker, apply heat to break it up.
Mount the slide in the vise with the right side toward the base of the vise and the bottom of the sights as close to the top of the jaws as possible. The closer they are to the jaws, the less flex you’ll get in the workpiece. The rear sights are a good place to start. They usually have a much larger flat area on the sides, so you can use a larger diameter punch to transfer more energy.
You might find that the dovetail cut on some slides is tapered; it’s easier to detect this and determine which direction it tapers on the rear sights. Pins are often installed from right to left, so it’s a good idea to first attempt to drift the sight out to the right. With the largest punch that fits inside the dovetail, place the face squarely against the sight. Full contact between the punch face and the workpiece spreads the load out and ensures maximum energy transfer.
While many people place the punch once and start wailing, try removing the punch between each strike to check for any damage (in the case of soft or cast sights), and then adjust your position or reset and hit it again. You don’t need to swing for the fences either; if you have a rigid setup, the sight should start to move quite easily. A firm 6- to 8-inch swing is typically all you need to break the static friction. If it doesn’t budge, increase your striking force gradually in small increments. If it doesn’t seem to get easier, or it doesn’t move at all, reverse the slide in the vise (so that you’re always hammering toward the base of the vise) and try from the other side.

This is what specialist aluminum punches look like after they’ve been used on handgun sights a few times. Save your money.
Once you get it moving, pay attention to the area that’s revealed as the sight moves to the side. On some pistols, there are small springs under tension beneath the rear sight. If you see the edge of a spring, move your pinky or ring finger over the hole while you push the sight to capture it.
The front sight will drift out in the same direction, but you’ll have less to work with, so you might need a smaller punch. The dovetail portion is typically quite shallow, so if you don’t feel comfortable striking it there, go as low as possible on the vertical portion of the sight. Avoid the inclination to place the edge of the punch on the dovetail, as it’ll usually swage the thinner material before it moves the sight. In this case, a flathead screwdriver might be better to increase the contact area on the dovetail or the bottom of the sight. The higher you strike the front sight, the more likely the sight post will bend or snap at the junction. Once the sights are removed, clean the dovetail slot with acetone and Q-tips.
INSTALLATION
Make sure you read the sight manufacturer’s documentation before you install them, in case there are any special instructions. Check the edges of the dovetails on the sights. If they seem sharp or don’t have a slight radius, you can hit them with a stone or some 320-grit sandpaper to achieve about a 0.005-inch radius. This will give the corners some clearance, so they don’t catch and gall in the dovetail cut.
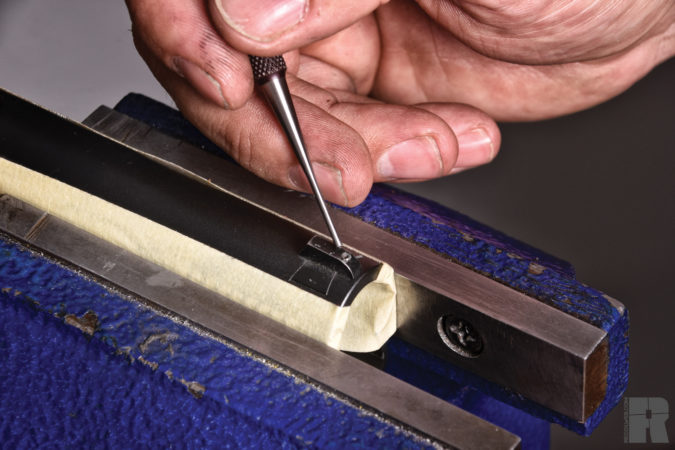
Don’t try to remove your front sight until you’re certain any set screw has been backed out.
Test-fit the sights by hand to see if they start in the dovetail without issue. A rule of thumb is that the pistol sights should slide in under finger pressure between one-third to just about halfway. If they do, remove the sights and apply a small amount of lube on the dovetail surfaces to prevent galling, then install them as far as they’ll go under finger pressure. Using the same technique as removal, drift the sights in until they align with any secondary retention devices or until it looks reasonably centered.
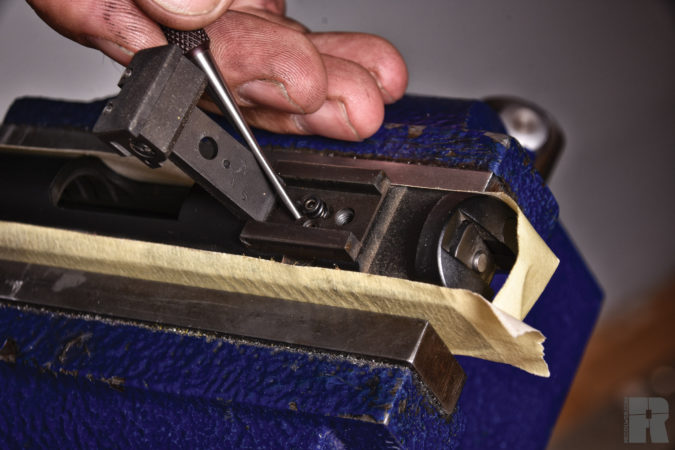
That goes for your rear sight, too.
If you find that the sight slips all the way through with little resistance, but doesn’t seem to be loose, don’t worry! You have two options. You can liberally apply some blue threadlocker to the dovetail cut, install the sight, and take the edge of a punch or a small screwdriver with a broad edge and swage the slide material to crimp the slide material down on the sight. Select a spot that’ll be hard to notice, preferably on either side of the vertical post of the sight. Then, wipe away excess threadlocker. However, if intentionally denting your slide is a little too extreme, you can try the threadlocker by itself, though this can have mixed results. When the threadlocker hardens, the crystalline structure is susceptible to cracking from the shock of the slide going into and out of battery.
If your sight goes in less than one-fourth of the way or doesn’t go in at all, first double check you have the correct replacement sight. If so, it’s time to bust out your file. Using the safe side up against the bottom of the sight post, gradually begin to remove material on only one side of the dovetail. Remember that your file only cuts one way, so don’t saw back and forth — this will kick up burrs that’ll mislead you during fitting, and you’ll end up removing too much material. Focus on smooth, linear strokes and follow the line of the material. Take three to five good swipes, wipe it clean, and check fitment. Continue this process until you can push the sight in far enough using finger pressure.
ALIGNMENT
Once you have both pistol sights installed and close to center, you can perform an initial alignment, assuming they aren’t constrained by some sort of secondary retention. Using the depth rod on your calipers, measure from the flat of the slide to the flat of the side of the sight. Then, take the same measurement on the other side of the slide. Calculate the difference between those two measurements and divide it by two. The result is how much farther you need to push the sight in from the side with the lesser measurement.
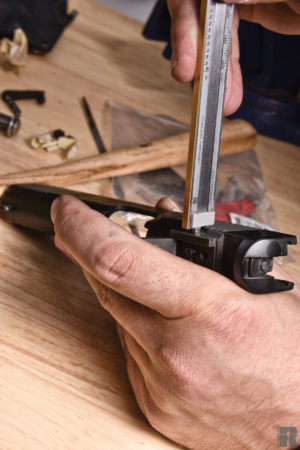
Use the tail of your caliper to ensure the sight is centered in its dovetail to get a working mechanical zero.
Small taps and a lot of patience are key. If your pistol sights seem like they stutter or jump when attempting small adjustments, apply localized heat with a propane torch. Concentrate the heat in front and behind the dovetail cut. Mechanical center is just an initial alignment because slides and barrels don’t always line up exactly when in full battery. Take a trip to the range to see where your rounds impact in order to make your final adjustments.
If rounds are landing left or right of where you’re aiming, you need to adjust windage, by drifting either the front or rear sight. Alternately, adjustable rear pistol sights may have a screw to adjust windage. If rounds hit high or low, adjust your elevation. With an adjustable rear sight, you can dial in the needed change. If it’s fixed, you’ll have to swap in a shorter or taller front sight to adjust your elevation.
If you’re good at math, you can calculate the necessary sight adjustments given your sight radius, distance to target, and deviation from point of aim to point of impact. Or just use the handy online sight calculators on Dawson Precision’s and Dillon Precision’s websites. During and after your first couple range trips, admire your handiwork and periodically check your pistol sights for any looseness or movement. Once you’re confident in your sights, grab some ammo and go get some!
More How-To’s and DIY Upgrades
Recoil