https://cdn.arstechnica.net/wp-content/uploads/2024/03/booted_mac_replica-760×380.jpg
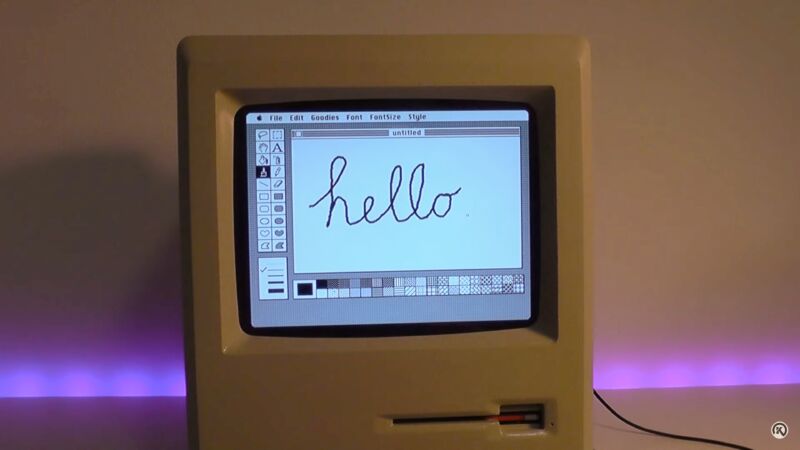
Kevin Noki
Have you ever worked on a hobby project where modifying and compiling the source code for a Linux-based emulator was possibly the easiest and most straightforward part of the whole thing?
Kevin Noki really, really wanted a functioning Macintosh Plus, complete with a functioning, auto-ejecting disk drive that it could boot from. The German maker already had a Mac Plus (1Mb) from eBay, but it had both a busted power supply and floppy drive. Rather than carve out the busted Plus’ one-of-a-kind internals and slap a Raspberry Pi in there like some DIY slacker, Noki went … a different path.
47 minutes and 25 seconds of a tour-de-force of modern maker technology.
Noki 3D-printed his own Macintosh, the "Brewintosh." I would like you to consider what you think that last sentence means and then wipe your expectations clean. I have watched the entire 48-minute journey of Noki’s Brewintosh, which is both very soothing on some ASMR-adjacent gut level and also low-key maddening for the way it plays down all the individual accomplishments along the way. Any one of the Brewintosh’s pieces would be my entire weekend, and my spouse would not enjoy my mood while I was sunk into it.
-
The design part of the Brewintosh, which you only see in super-fast time-lapse summary, but which is pretty, pretty notable.
-
Now the custom board-building, circuit design, and internal space configuration can begin!
-
The tiny two-part board Noki built to rework serial and ADB input to USB is pretty much its own project (and video).
-
Detail on the Brewintosh sticker and corner of the finished project.
But Noki, over what he reports as "months," essentially works backward from 2024, using every kind of maker tool and skill to get back to a working 1986 Mac. Not just "classic Mac OS on a properly sized AliExpress monitor," mind you. We are talking a properly sized, colored, and textured box, which takes wall power, swallows 3.5-inch disks, works with both telephone-cord and ADB Apple keyboards and mice, has a screen dimmer, and makes the startup sound (the beep, not the chord). It’s not a "loving" tribute, it’s uncanny and potentially unnerving.
If you wanted a non-historic but ultra-authentic Mac like Noki’s, this is the somehow-not-exhaustive list of 29 things for which you would have to have the tools, skills, and patience:
- Meticulously measuring every single surface and angle of a Macintosh Plus
- Re-create those measurements and model them in AutoDesk Fusion 360
- Print the Mac case in four parts using a modified Ender-3 with gray PLA filament
- Apply one-part plastic filler and sand down the planes where the case pieces would join
- Drill registration holes in the case parts for metal pin connectors
- Use cyanoacrylate (CA) glue to join pieces and repeatedly sand every part with 3D layers showing
- Spray-paint both a primer and final beige color on the outward-facing parts
- Use a vinyl cutter to protect the case parts that should be smooth
- Apply textured clear-coat to replicate the Mac’s rough texture
- Disassemble a 10-inch screen that was a thrift-store find
- Replace the screen’s CCFL with LED lighting
- Rewire and solder a dimmer knob onto the screen to create a dimming control
- De-solder and modify a laptop charging brick to make a power assembly
- Modify a powered USB hub and its AC adapter
- Dye a physical power switch to match its proper case color
- Use WAGO connectors to connect power components safely
- Disassemble a $13 thin client computer and replace its power jack with an XT60
- Wire in a resistor to make that power supply work with an outside adapter
- Replace the thin client’s power button with an Arduino-controlled relay
- Build a front keyboard and mouse connector out of a Teensy USB dev board, RJ11 jack, and TMK keyboard firmware.
- Solder and wire in an internal speaker
- Rebuild a USB floppy drive reader with an Arduino-controlled stepper motor (that you coded) to eject disks from software controls
- Built an ADB peripheral board with a KiCAD design, a Teensy board, and an Arduino Pro Micro
- Configure an ATtiny85 to control mainboard and screen power, and play the startup sound
- Build a modified Mini vMac emulator inside a Linux system
- Design your own Brewintosh raised-text stereotype and apply foil to it with a laminator
- Create custom-designed Brewintosh multicolor stickers, print them, apply UV resin for a glossy finish, and cure them
- Design and print a replica sticker of the original Mac’s back panel
- Record yourself doing all these things and edit them into an engaging video.
I didn’t include the smaller ("smaller") things Noki 3D-printed in that list because I respect your scroll fingers. You also have to design and accurately print at least 12 other components. That list includes the feet in resin, a screen board holder, an inner frame, power assembly cover, power cabling routing box, audio jack holder, USB port and SD card holder, internal speaker chassis, disk drive stepper motor attachment, manual disk eject, the brightness control dial, and probably a dozen tiny things Noki doesn’t even mention.
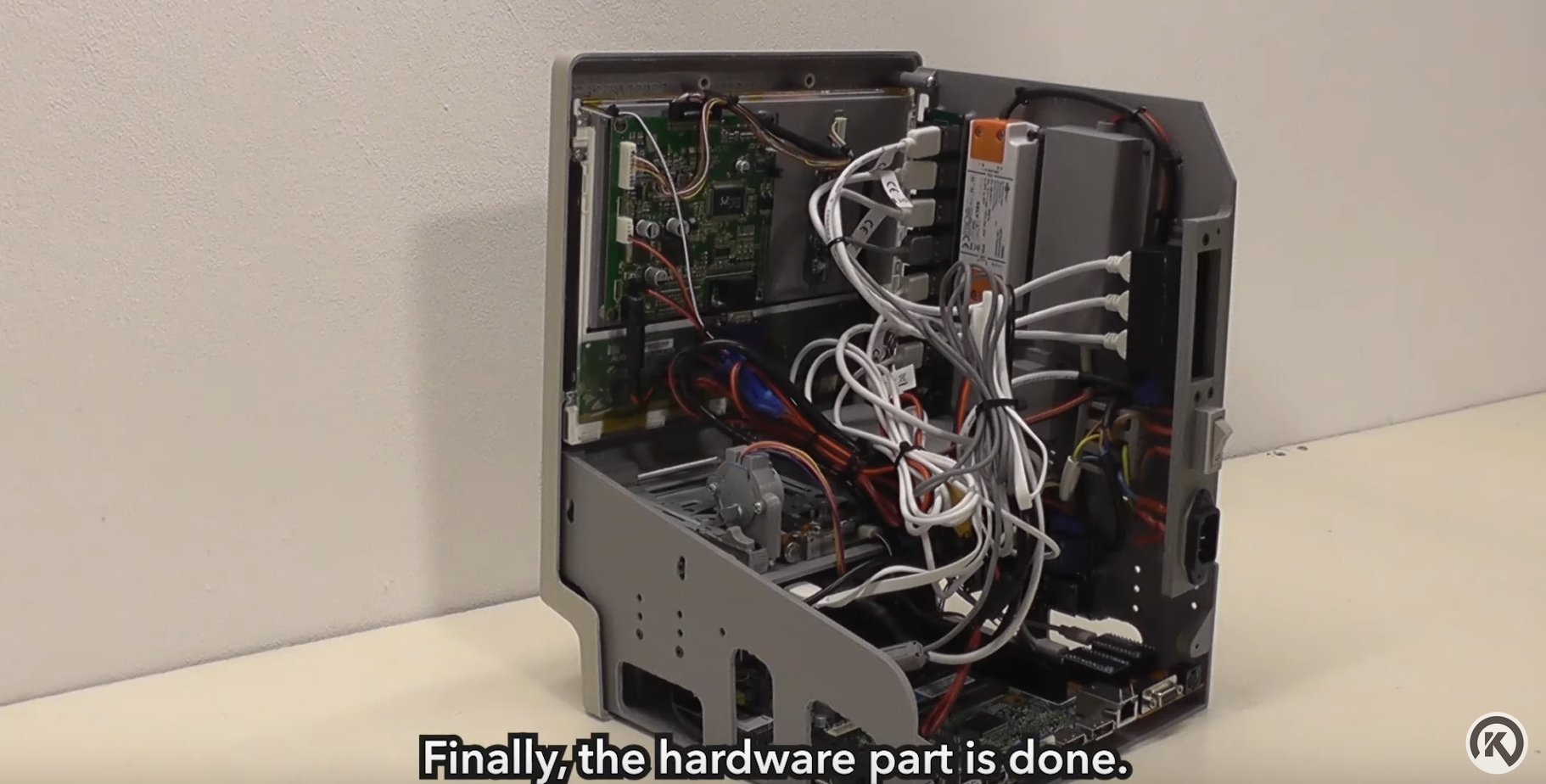
I am not actually suggesting anybody with a biologically limited lifespan attempt what Noki has done here. If you tackled each component and 3D-printed part as individual weekend projects, it adds up to more than 40 weeks. Mind you, printing the 3D parts alone took 48 hours, according to Noki. But even that spread presumes that you’re starting from the obvious familiarity Noki has with all his printers, cutters, and tools. He doesn’t include any mistakes or missteps in his video, but you just know in your heart that you would reach a certain point in the assembly and realize that something just doesn’t fit at all, so you must go back and do it, and possibly two or three other whole things, again.
Watching this video did a number on me. Seeing the astounding number of skills on display, paired with the Steven Jobs-like attention to detail, can be overwhelmingly intimidating or simply affirming and wonderful, depending on how you take it in. Someone in the YouTube comments points out a little bit that Noki himself doesn’t even mention in his subtitle text: that the monitor stays off until the vMac emulator has started and produced the tiny smiling Mac icon. All of that, just to get to the point where you can play 3D chess or use MacPaint in a little beige time machine.
Ars Technica – All content